
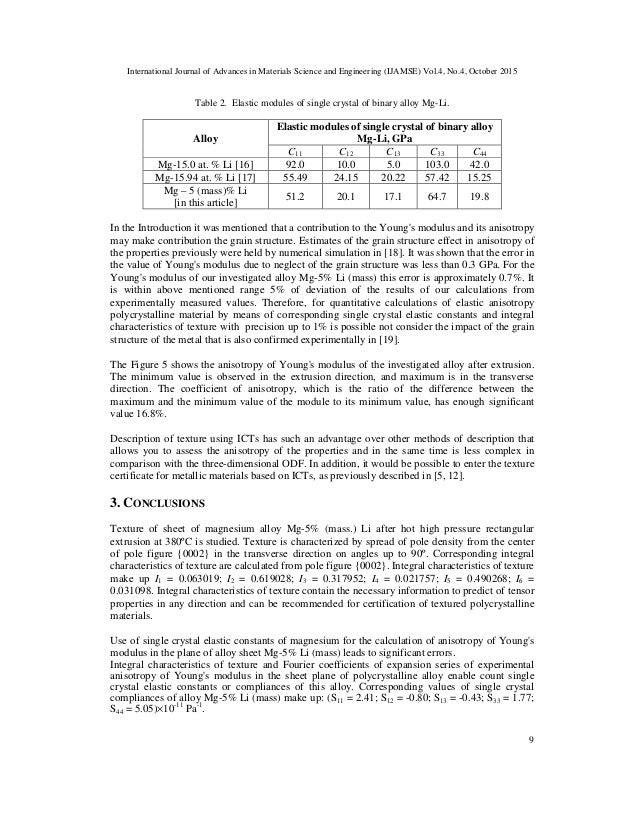
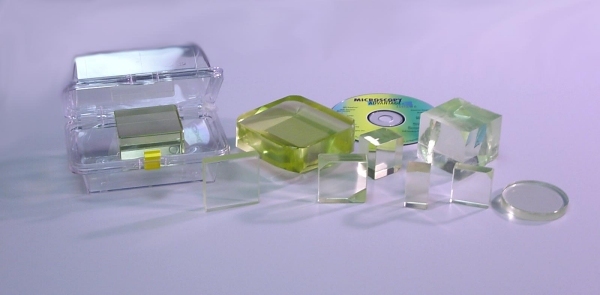
The form of the hardness impression very well depicts changes in the mode of deformation of MgO over different temperature ranges. Yield strengths at known strains are obtained from the hardness measurements and are presented. By this means the hardness of the hardest materials can be measured at very high homologous temperatures. This method, which involves pressing together two similar crossed specimens, overcomes the problem of finding materials sufficiently rigid and chemically stable for use as indenters in conventional quasi‐static methods of indentation hardness testing. The mechanical properties of single crystals of MgO were measured from 600° to 1700° C using the mutual indentation hardness technique. Diffraction patterns are rotated to place the (2,0,0) diffraction spots on the horizontal axis. With high optical damage resistance and homogeneity, MgO:LN wafers (upto 4 inches in diameter) are now being used in new applications in the optical network, blue laser and other markets.Mutual Indentation Hardness of Single‐Crystal Magnesium Oxide at High Temperatures Mutual Indentation Hardness of Single‐Crystal Magnesium Oxide at High Temperatures 100-zone diffraction patterns of singlecrystal MgO compressed in a helium pressure medium at 40 and 110 GPa (upper panels) and in a KCl pressure medium at 7.4 and 80 GPa (lower panels) taken with monochromatic synchrotron radiation at 45 keV.
#SINGLECRYSTAL MAGNESIUM FREE#
Over this time the focus has been on optimising growth conditions and improving raw material purity (to avoid impurities such as Fe) with the result that sub-grainboundary free material is now readily available with excellent transmission characeristics. Magnesium Single Crystal Poissons Ratio, 0.29 Specific Heat, 0.243 Cal/g/K 25 C Tensile Strength, N/A Thermal Conductivity, 1.56 W/cm/K 298.2 K. At shorter wavelengths, for example with blue lasers, the photorefractive effect must also be considered – here we can see local changes in the refractive index in areas under laser illumination which lead to optical damage.ĭevelopment and manufacture of MgO:LN has taken place since 1985. In general, the main requirement for MgO:LN for optical applications is a stable and homogeneous refractive index ( Erbium doping is also available). The characteristics of Magnesium doped lithium niobate are resistance to optical damage, low absorption loss and no refractive index fluctuation within the crystal. To control these phenomena, high optical damage threshold materials have been developed, using magnesium as a dopant. Compression of single-crystal magnesium along the 0001 direction at room temperature confirmed a high yield stress, high work-hardening and minimal. It is well known that applying a short wavelength (blue or green) laser to lithium niobate causes "optical damage" through the photo-refrective effect, and also refractive index fluctuations. Magnesium Doped Lithium Niobate for PPLN - (Periodically Poled Lithium Niobate) To improve the quality of optical grade, we aim to achieve sub-grain boundary free wafer. This is a very simple way to control the crystal quality to determine whether whether Optical or Saw grade. Quality Control level of refractive index For quality control purposes, these figures are a measurement to achieve high quality as standard. These data confirm a total cross section that is lower than that of MgO for wavelengths greater than 0.2 nm. There is significant correlation between refractive index and composition. The neutron attenuation through single-crystal magnesium fluoride has been measured as a function of wavelength at both room temperature and 77 K. Quality Control level of Curie temperatureĢ Evaluation Using Refractive Index- Related to the composition of LiNbO3 / LiTaO3 The Roditi International Corporation LtdĮvaluation and Quality Control for Optical Wafers 1 Evaluation Using Curie Temperature - Related to the composition of LiNbO3 / LiTaO3.
